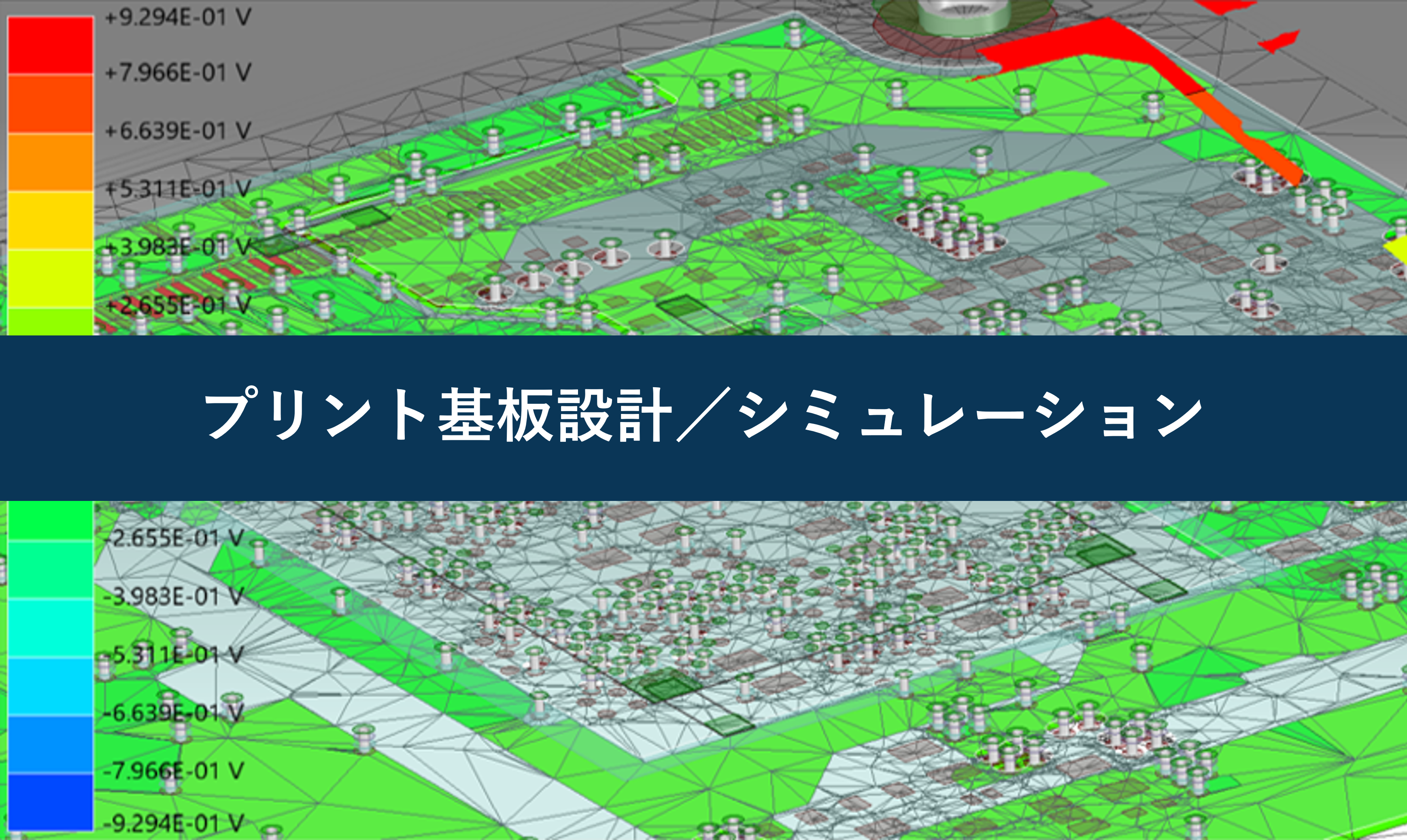
SI解析で基板設計も短期化・高品質化を実現
近年、電子機器の発展に伴いプリント基板の高密度化・信号の高速化等が飛躍的に進んでおり、プリント基板には高い品質が求められています。基板を製造する前の設計段階で「シミュレーション」を行うことにより、電気的により良いものを作ることが可能になり、…
近年、電子機器の発展に伴いプリント基板の高密度化・信号の高速化等が飛躍的に進んでおり、プリント基板には高い品質が求められています。基板を製造する前の設計段階で「シミュレーション」を行うことにより、電気的により良いものを作ることが可能になり、…
12G-SDIはSMPTE ST 2082にて規格が確立されており、その中のうちの一つにリターンロス特性の要求値があります。リターンロスとは反射損失のことで、伝送する進行波と反射波の比をデシベルで表現し、12G-SDIは周波数帯域毎にスペッ…
昨今の電子機器分野では、LSIの高性能化に伴う消費電力の増加や機器の小型化が相まって、部品パッケージサイズのシュリンク、プリント基板の高密度化が進行しており、熱を逃がすためのスペースは縮小傾向にあります。それらの影響から、従来の設計手法では…
FPGA需要の増加 IoTとAIの台頭やカスタマイズ可能なソリューションに対する要求の増加により、FPGA市場価値は上がっており、日本では産業オートメーションやロボット工学の成長により需要が高まっていることは周知の事実であります。複雑化する…
短納期かつ高品質を誇るキョウデンの製品。その秘密の一つとして、データ受入体制の確立で生産工場を支えるCAMセンターの存在があります。60名以上のCAM編集者が、お客様から支給されたガーバーデータを即時に製造可能なデータに編集を行います。特に…
キョウデンは、EV、AGV等の充電方法の一つであるワイヤレス給電システム(停車中ならびに走行中)に用いられる銅コイル基板の開発を行っており、本技術を用いてトランス用の銅コイル基板では量産対応も行っております。 2030年のSDGs目標達成に…
キョウデンは、電子機器の高機能及び小型化が進み高密度・高集積半導体の採用に直面する様々な課題解決に向け狭隣接実装技術を確立しました。新製品の開発が加速する5G/6G情報端末、IoT端末、先端医療機器、非接触型サービスロボット、高速センシング…
基板の銅箔は上下に隣接していると共振というものが発生します。つまり並行平板のパッチアンテナとして機能してしまうということです。また、銅箔で形成されたプレーンの大きさや形によって、共振する周波数は様々で、例えば電源の小さなリップルノイズの周波…